~ CNC Machining: lathe tools explained ~
Lathe tools are the cutting tools that are mounted on a lathe (wood/hand/CNC) application to produce turned parts. The tools move along the axis of the lathe and the path they take determines the final shape of the piece. As there are several options for lathe cutting tools, for both CNC and non-CNC, you need to understand the tools and what features and applications they are suited to.
What is a lathe?
A lathe is a machine tool that rotates (or turns) a workpiece around an axis of rotation, with different tools required to cut the metal into a final symmetrical part or component. Modern lathes are CNC (computer numerically controlled), and the turning process can be implemented on an external surface of the workpiece or internally. Lathes are used in a wide range of manufacturing and production operations, creating components or rounded parts of various sizes, often to be used within a wider final system, such as piston supports to be used within a car engine.
What are the different categories of lathe cutting tools?
There are generally four categories when it comes to types of lathe cutting tools for both CNC and non-CNC.
Cutting tools based on material
Many materials are suitable to be used on a lathe, but each will have its own characteristics, meaning there is a corresponding cutting tool that is best used with each material type.
HSS (High-speed Steel)
Containing elements such as carbon, tungsten, chromium, and vanadium, high-speed steel is used to make cutting tools that are extremely strong, hard, and have great wear and heat resistant properties. For machining that is rougher and has a semi-finish, this is a suitable option.
Carbide
Carbide lathe cutting tools are compatible with most materials due to its hardness.
Diamond
These have extreme hardness properties and are therefore suitable to work with all material types. They are expensive to run, so limited in use.
Cubic Boron Nitride
These are suitable for machining that is rough, for cutting that is intermittent, as they are robust and abrasion resistant.
Cutting tools based on operations
Cutting tools are also categorised used on the operation being used.
Turning tools
Turning tools are used in removing materials along the length of the workpiece. These are rough turning tools to remove large amounts in a single pass and finish turning tools to remove small amounts to create a smooth, finished surface on the piece.
Chamfering tools
These are suitable for producing pieces with a slanting edge. Although turning tools are used for this application, they must be set to match the angle of the workpiece, adding an extra layer to the process.
Thread cutting tools
These are suitable for spiral thread patterns as well as parts that are cylindrical. The nose angle will be determined by the angle of the thread.
Facing tools
Utilising the side cutting edge, a thin layer of materials can be removed to produce a smooth finish on the surface.
Grooving tools
Used to make grooves on a workpiece with a cylindrical surface. Common shapes of grooves include V-shaped and square cutting tools.
Forming tools
This is a combination of a turning and a grooving tool to make complex shapes in one go, increasing accuracy and reducing cycle time.
Boring tools
A boring bar that has a cutting tool at the end is used to increase the size of the hole in diameter.
Knurling tools
Knurling tools are used to produce indents to increase the grips on the workpiece. It has metal rolling wheels with embossed patterns.
Cutting tools based on structure
There are three types of lathe cutting tools based on their structure.
Single body tools
These are manufactured from a single piece of material, designed in a specific size, shape, and geometry. Used for their speed and strength and are the most common lathe machine tool.
Welding tools
These tools are welded together from different materials, bringing the head and rod together as one piece.
These tools have a head and rod made from different materials and welded together. The flank comes from a material that offers robustness and durability, whilst the body can be made from a variety of materials.
Clamp lathe cutting tools
Similar to welding tools, but the clamp tool is formed by placing the insert on a handlebar. They are replaceable and dexterous, and the strength and lifecycle will depend on the inserts used.
Lathe cutting tools based on feed direction
Three types of lathe cutting tools based on the direction of the feed are:
Right-hand cutting tools
Materials are removed when transporting from right to left, with a design similar to a human hand, with the right thumb indicating the direction of the feed and the main cutting edge on the left.
Left-hand cutting tools
These tools are exactly the same as above, but in the opposite direction, transporting from left to right, with a left thumb and a cutting edge on the right.
Round nose cutting tools
They can move from left to right and right to left, with no side rake and back rake angles. Suitable for those operations where a smooth surface is required.
Common components of a lathe cutting tool
The following parts of common to every type of lathe cutting tool:
- Shank – connected to the lathe, the thickest part of the tool
- Face – the part which the chip flows during operations
- Flank – Opposes and interacts with the workpiece
- Cutting edge – responsible for the cutting action
- Tool nose – this offers a smoother cut due to the design of the curvature on the main and minor cutting-edge intersection
- Side rake angle – determines the direction of chip flow
- Side relief angle – prevents the major flank from rubbing against the workpiece
- End relief angle – prevents the minor flank from rubbing against the workpiece
- Back rake angle – A high rake angle increases sharpness but decrease strength, and vice versa
- End cutting edge angle – prevents the tool from touching the machined surface of the workpiece
- Side cutting edge angle – important in cutting force and chip thickness during lathing operations
How to choose the correct lathe cutting tool
Choosing the right lathe tool will always depend on the application, the type of component being produced, its complexity and size, along with the material that is being machined. Simple components and materials will need a simple lathe, whereas more complex components will require more complex machines and larger workpieces to offer stability and accuracy. The cutting power is also important, as harder materials will require a heavy-duty machine to provide the required rigidity.
This guide has given you all the basic points of understanding about lathe tools and how to choose the correct machine for your operations.
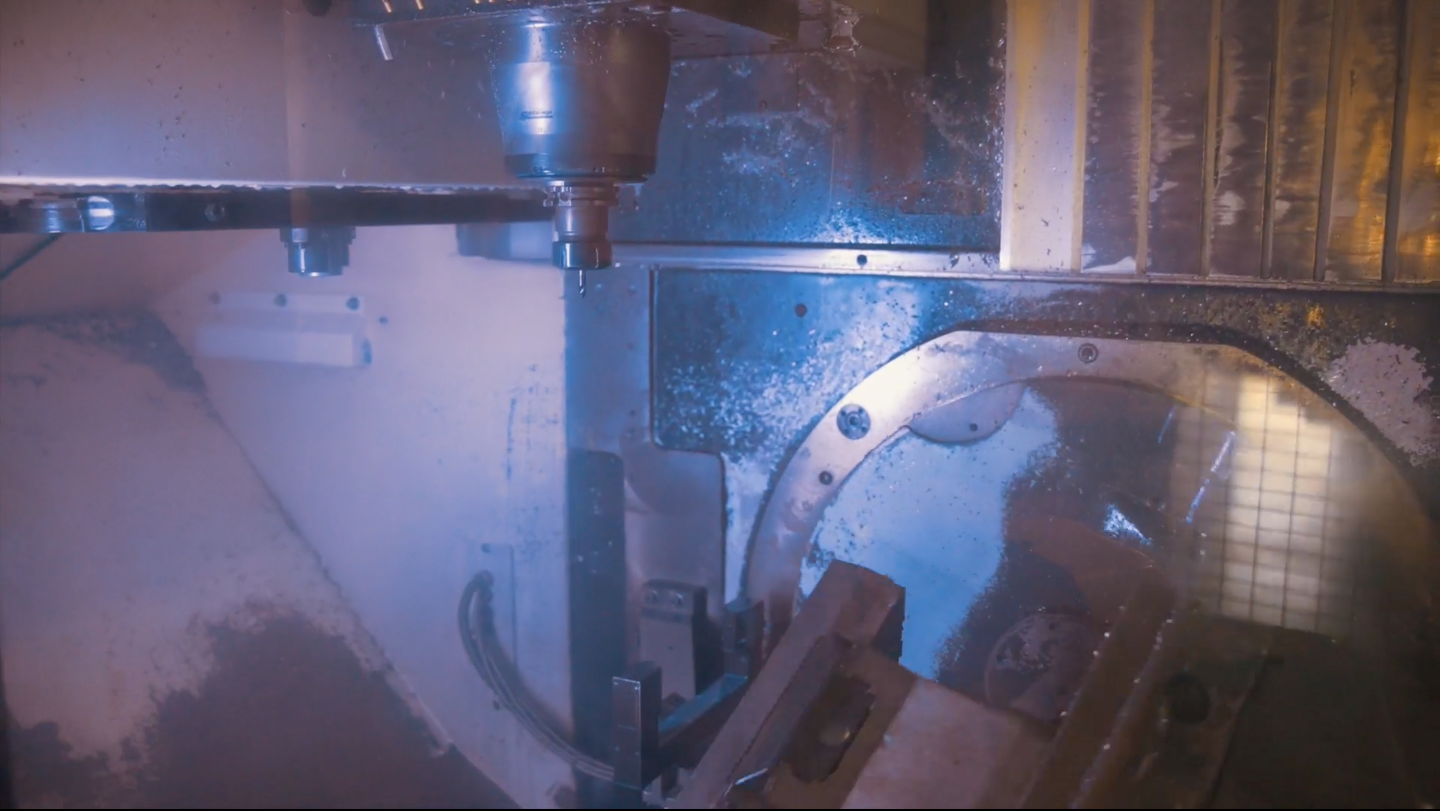
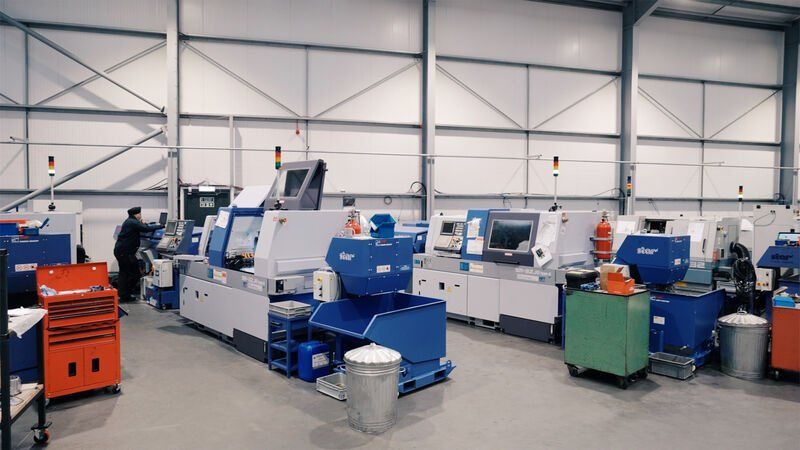
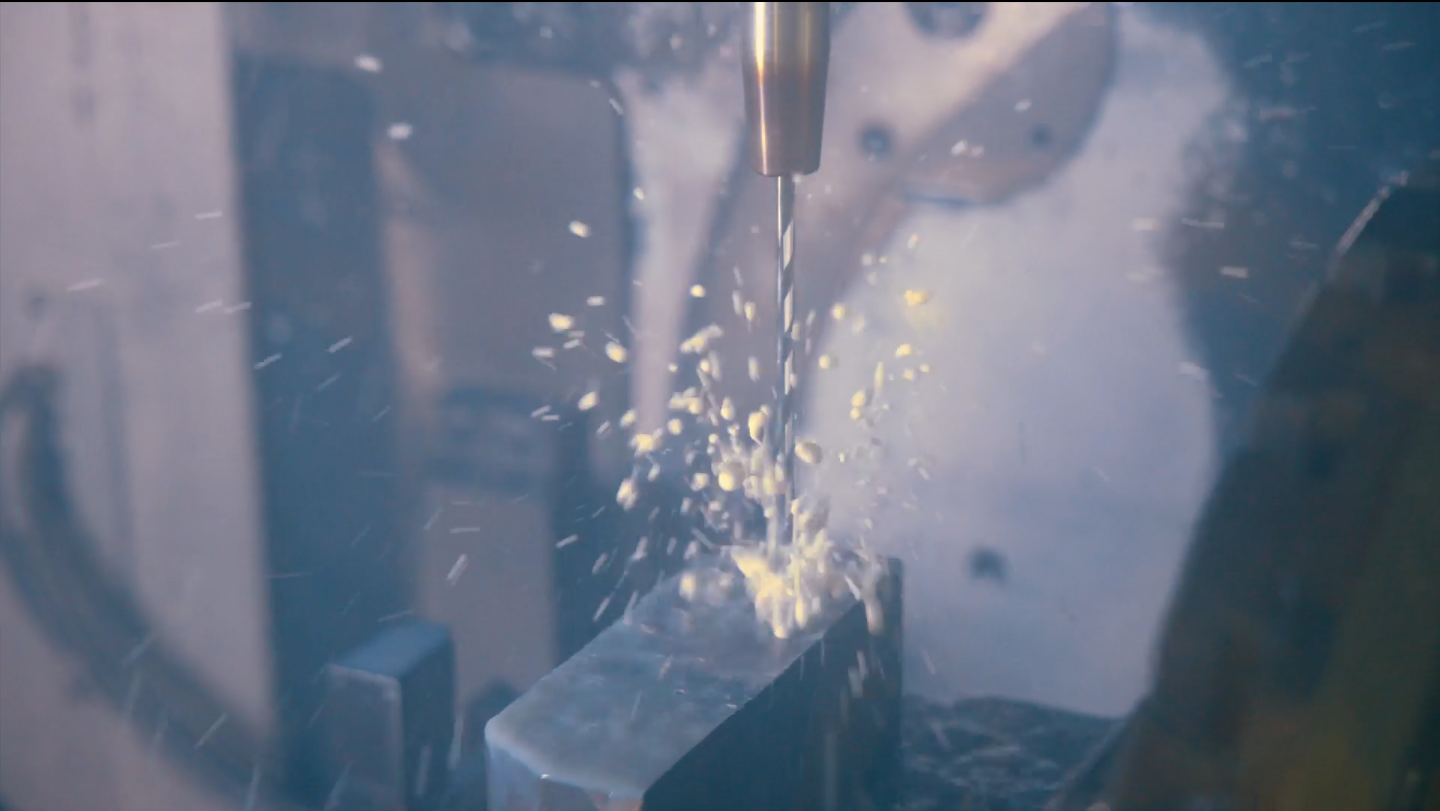
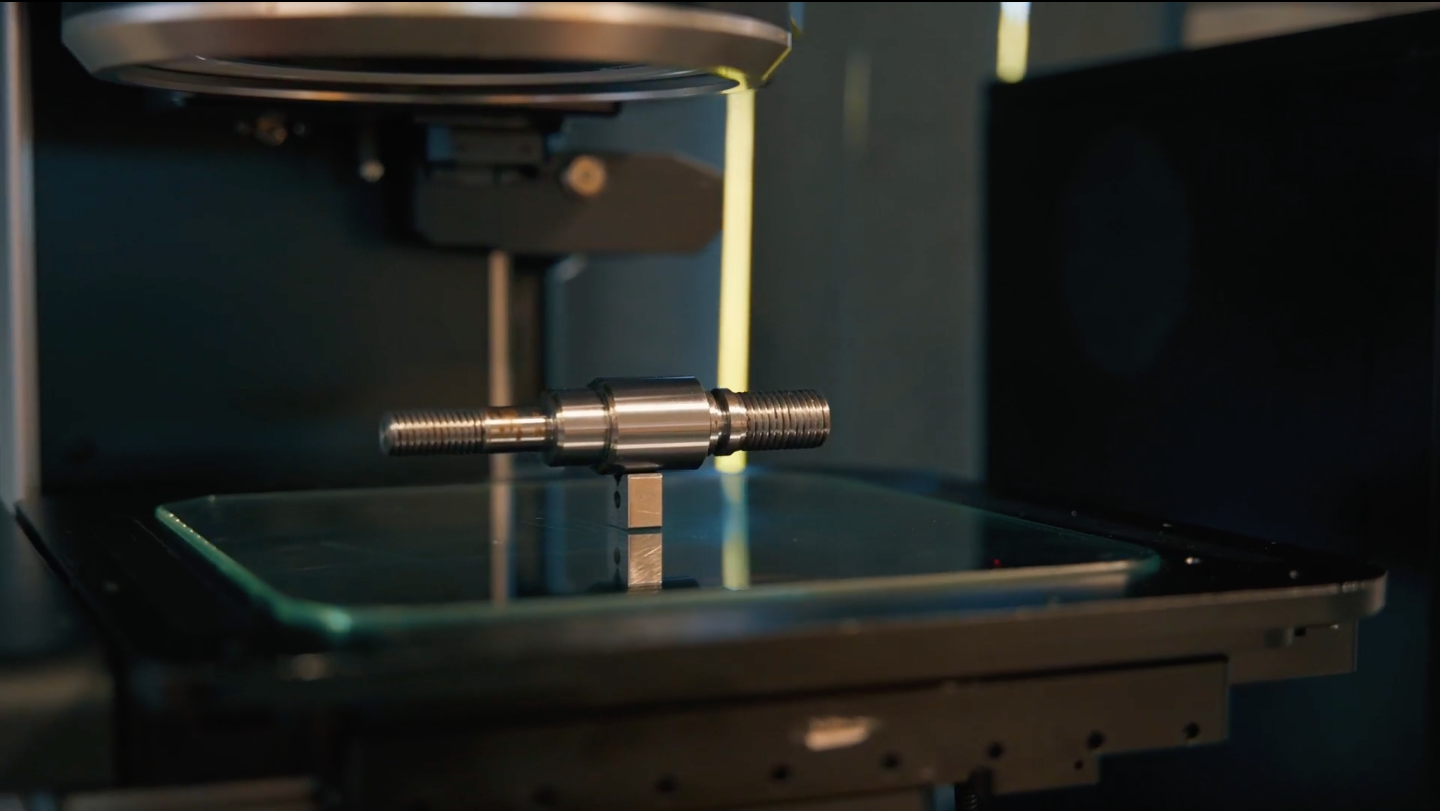