~ A Guide to CNC Machine Operations ~
Having a better idea of CNC machine operations helps professionals stay competitive in a rapidly evolving manufacturing landscape.
CNC machines have revolutionised the manufacturing landscape by enabling the mass production of components with consistent quality and reduced lead times. From automotive and aerospace to electronics and medical devices, CNC machining is widely adopted across various sectors to manufacture complex parts and components.
But, ever wondered how CNC machines work? What are the different types of CNC machines and how are they used? If you have had these questions in your mind, you have come to the right page! In this article, we offer you a basic understanding of the various aspects of CNC machine operations. But before we dive in, let's understand why this information is essential for manufacturing professionals.
Why Having a Basic Understanding of CNC Operations Matters
For manufacturing professionals, having a basic understanding of the operation of CNC machines is indispensable for several reasons:
- Improved Production Efficiency: By gaining insights into CNC machine operations, you can streamline production processes, reduce lead times, and increase output.
- Cost Reduction Opportunities: Having better control of CNC operations can lead to cost savings through improved resource allocation, reduced material wastage, and optimised machine utilisation.
- Competitive Advantage: Proficiency in CNC operations can give manufacturing professionals a competitive edge in the market by offering higher quality products, faster turnaround times, and greater flexibility in meeting customer demands.
- Informed Decision-Making: A thorough understanding of CNC operations empowers professionals to make informed decisions regarding equipment investments, process optimisations, and workforce training, leading to enhanced operational efficiency and business growth.
- Adaptability to Technological Advances: Manufacturing professionals can stay ahead of the curve by keeping abreast of advancements in CNC technology and leveraging new capabilities to drive innovation.
Key Components of CNC Machines
CNC machines comprise several key components that work together to execute machining operations with precision and efficiency. These include:
- Control Panel: The control panel serves as the interface for operators to input commands and control machine functions, facilitating adjustments to parameters such as spindle speed, feed rate, and toolpath.
- Motors and Drives: Motors and drives function as power sources that propel the movement of machine components, including axes and spindles. They ensure precise and coordinated motion control, leading to accurate positioning and machining results.
- Worktable: The worktable acts as the surface on which the workpiece is securely mounted and machined. It may be equipped with fixtures, clamps, or vacuum systems to effectively secure the workpiece during the machining process.
- Cutting Tools: Cutting tools, such as drills, end mills, and lathe tools, are instrumental in removing material from the workpiece to shape it according to the programmed design. These tools come in various types and sizes, catering to different materials and machining operations.
Understanding these key components is essential for operating and maintaining CNC machines effectively. Each component plays a critical role in the machining process, and familiarity with their functions and interactions is vital for achieving optimal performance and productivity.
Different Types of CNC Machines and Their Operations
Understanding the operational overview of different types of CNC machines is essential for selecting the right tool for specific applications and maximising machining efficiency in manufacturing processes. Let’s have a brief look at them, one by one.
CNC Mills
These versatile machines operate by rotating cutting tools against a stationary workpiece, removing material to achieve desired shapes and dimensions. They are ideal for milling, drilling, and cutting operations, making them suitable for producing mechanical parts, moulds, and prototypes.
CNC Lathes
Operating by rotating the workpiece while a cutting tool removes material, CNC lathes are designed for turning cylindrical workpieces. They excel in producing rotational parts like shafts, pins, and fittings, offering precision and efficiency in turning, facing, drilling, and threading operations.
CNC Routers
CNC routers operate by moving a rotating cutting tool along multiple axes to remove material from the workpiece. They are versatile machines used for cutting, carving, and engraving various materials such as wood, plastics, and composites. Widely employed in woodworking, signage, and prototyping industries, CNC routers offer precise and intricate machining capabilities.
CNC Plasma Cutters
Utilising a high-velocity jet of ionised gas (plasma), CNC plasma cutters melt and remove material from metal plates and sheets. They excel in cutting various metals with exceptional accuracy and efficiency, making them indispensable in industries such as automotive, construction, and metal fabrication.
Now, that we have a basic overview of CNC machines and their operational uses, let’s have a look at how they are operated.
Preparing for CNC Machine Operations
Ensuring Safety
The safety of both personnel and equipment is of the highest concern when operating the machinery. CNC machine operators must adhere to strict safety protocols to mitigate risks and prevent accidents. This includes wearing appropriate personal protective equipment (PPE) such as safety glasses, gloves, and hearing protection. Additionally, CNC machines should be equipped with safety features such as emergency stop buttons, interlocks, and machine guards to safeguard operators from potential hazards.
Material Selection and Workpiece Setup
Selecting the right material and setting up the workpiece correctly are critical steps in CNC operations. Manufacturers must consider factors such as material properties, dimensions, and tolerances when choosing the material for machining. Proper workpiece setup involves securely mounting the material on the machine's worktable using clamps, vises, or fixtures to ensure stability during machining. Additionally, selecting the appropriate cutting tools and toolpaths is essential for achieving desired machining results while minimising material waste and tool wear.
Setting Up CNC Machines
Proper setup of CNC machines is crucial for achieving optimal results and ensuring operator safety. This includes calibrating machine parameters, aligning axes, and verifying tool offsets to meet machining requirements. It's important to follow the set guidelines and best practices for machine setup to minimise errors and maximise accuracy and efficiency.
Tool Setup and Calibration
Tool setup and calibration are essential steps in CNC machining to ensure proper tool performance and machining accuracy. This involves selecting the appropriate cutting tools, correctly installing them in the machine's tool holders, and calibrating tool offsets and lengths to compensate for tool wear and variations. Additionally, manufacturers should establish regular tool inspection and maintenance procedures to prolong tool life and maintain machining quality.
Loading and Running of Programs
Proper loading and running of CNC programs are essential for maximising production throughput and minimising downtime. This includes properly loading programs into the machine's control system, verifying program correctness and integrity, and simulating machining processes to detect potential errors before actual production runs. Manufacturers should also implement strategies such as batch processing, toolpath optimisation, and machine scheduling to optimise production efficiency and meet production targets.
Operating CNC Machines
Navigating Machine Control Interfaces
Operating CNC machines requires familiarity with the machine control interface, which typically consists of a screen displaying various controls and commands. Professionals must understand how to navigate through menus, input program codes, and execute commands effectively. Additionally, knowledge of emergency stop procedures and manual overrides is essential for maintaining safety and responding to unexpected situations.
Monitoring Processes for Quality Assurance
Continuous monitoring of machining processes is crucial for ensuring product quality and consistency. Professionals should closely monitor machine parameters, tool wear, and surface finish during operations to identify any deviations from desired specifications. Implementing real-time monitoring systems and quality control measures enables timely adjustments and interventions to maintain production standards and prevent defects.
Addressing Common Operational Challenges
Despite meticulous planning and preparation, CNC machining operations may encounter challenges such as tool breakage, material deformation, or programming errors. Professionals must be equipped to troubleshoot these issues promptly and effectively. This involves diagnosing the root cause of the problem, implementing corrective measures, and adjusting machining parameters as necessary to resume production smoothly.
Maximising Performance of CNC Machines
Optimising Toolpaths for Efficiency
Optimising toolpaths is essential for maximising machining efficiency and minimising cycle times. Advanced CAM software offers features such as toolpath optimisation algorithms and adaptive machining strategies to optimise tool movements and minimise air cutting. By strategically planning toolpaths and minimising unnecessary movements, professionals can reduce machining times and improve overall productivity.
Maintenance for Long-term Usage
Regular maintenance is critical for prolonging the lifespan of CNC machines and ensuring consistent performance. Professionals should adhere to manufacturer recommendations for routine maintenance tasks such as lubrication, cleaning, and calibration. Implementing a proactive maintenance schedule helps prevent unexpected downtime, reduces repair costs, and extends the service life of critical machine components.
Achieving Precision and Accuracy to Meet Standards
Achieving precision and accuracy is of prime importance in CNC machining, especially for industries with stringent quality requirements. Professionals should pay attention to factors such as machine calibration, tool wear compensation, and workpiece positioning to ensure dimensional accuracy and surface finish. Implementing metrology tools and quality assurance procedures enables verification of part dimensions and adherence to specifications, ensuring compliance with industry standards and customer expectations.
Programming Essentials for CNC Machining
Overview of CNC Programming Concepts
CNC programming involves creating instructions (G-code and M-code) that control the movements and actions of the CNC machine during machining operations. Manufacturing professionals need to understand basic programming concepts such as coordinate systems, toolpath generation, and tool compensation to effectively program CNC machines.
Understanding G-code and M-code
G-code is a programming language used to control CNC machines by specifying commands for movements, speeds, and tool operations. M-code, on the other hand, controls auxiliary functions such as coolant activation, spindle speed, and tool changes. Manufacturing professionals must familiarise themselves with common G-code and M-code commands to program CNC machines accurately and efficiently.
Utilising CAD/CAM Software for Production Efficiency
Computer-Aided Design (CAD) and Computer-Aided Manufacturing (CAM) software are essential tools for generating CNC programs and optimising machining processes. CAD software allows users to create 2D and 3D models of parts and assemblies, while CAM software generates toolpaths and generates G-code for CNC machines. Manufacturing professionals can leverage CAD/CAM software to streamline design and production workflows, reduce programming time, and improve overall production efficiency.
Advanced CNC Techniques
Advanced CNC techniques offer manufacturers the ability to push the boundaries of traditional machining processes and differentiate themselves in the market. These techniques encompass a wide range of advanced machining strategies and technologies, including:
Multi-axis Machining: Utilising CNC machines with multiple axes (such as 4-axis or 5-axis machines) enables manufacturers to machine complex geometries and achieve intricate part features with greater efficiency and precision.
High-Speed Machining: High-speed machining techniques leverage advanced cutting tool materials, toolpath optimisation algorithms, and machine dynamics to increase cutting speeds and feed rates, resulting in shorter cycle times and improved surface finish.
Adaptive Machining: Adaptive machining strategies dynamically adjust cutting parameters in real-time based on machine feedback and part geometry, optimising material removal rates, reducing tool wear, and improving process stability.
Additive Manufacturing Integration: Integrating CNC machining with additive manufacturing technologies such as 3D printing enables manufacturers to produce hybrid parts with complex geometries and tailored material properties, expanding design possibilities and reducing lead times.
Digital Twin Simulation: Digital twin simulation technologies enable manufacturers to create virtual replicas of CNC machines and manufacturing processes, facilitating predictive maintenance, process optimisation, and performance monitoring to maximise operational efficiency and uptime.
By utilising these advanced CNC techniques, manufacturing professionals can drive innovation, improve productivity, and gain a competitive edge in an increasingly dynamic and demanding manufacturing landscape.
Final Thoughts
By understanding the fundamentals of CNC machines, exploring advanced techniques, and implementing best practices for machine setup and operation, professionals can unlock new opportunities for efficiency, innovation, and growth. Whether you're a novice or a seasoned expert, continuous learning and adaptation are key to success in the dynamic world of
CNC machining.
At Rotec, we specialise in complex CNC machining and bring decades of combined precision engineering experience to the table. We offer manufacturing solutions tailored to each project's specific requirements. With our state-of-the-art technology, a team of seasoned experts, and a commitment to excellence, we're here to help you stay ahead of the competition and achieve your manufacturing goals. Don't settle for anything less than the best.
Contact us today to discuss your requirements!
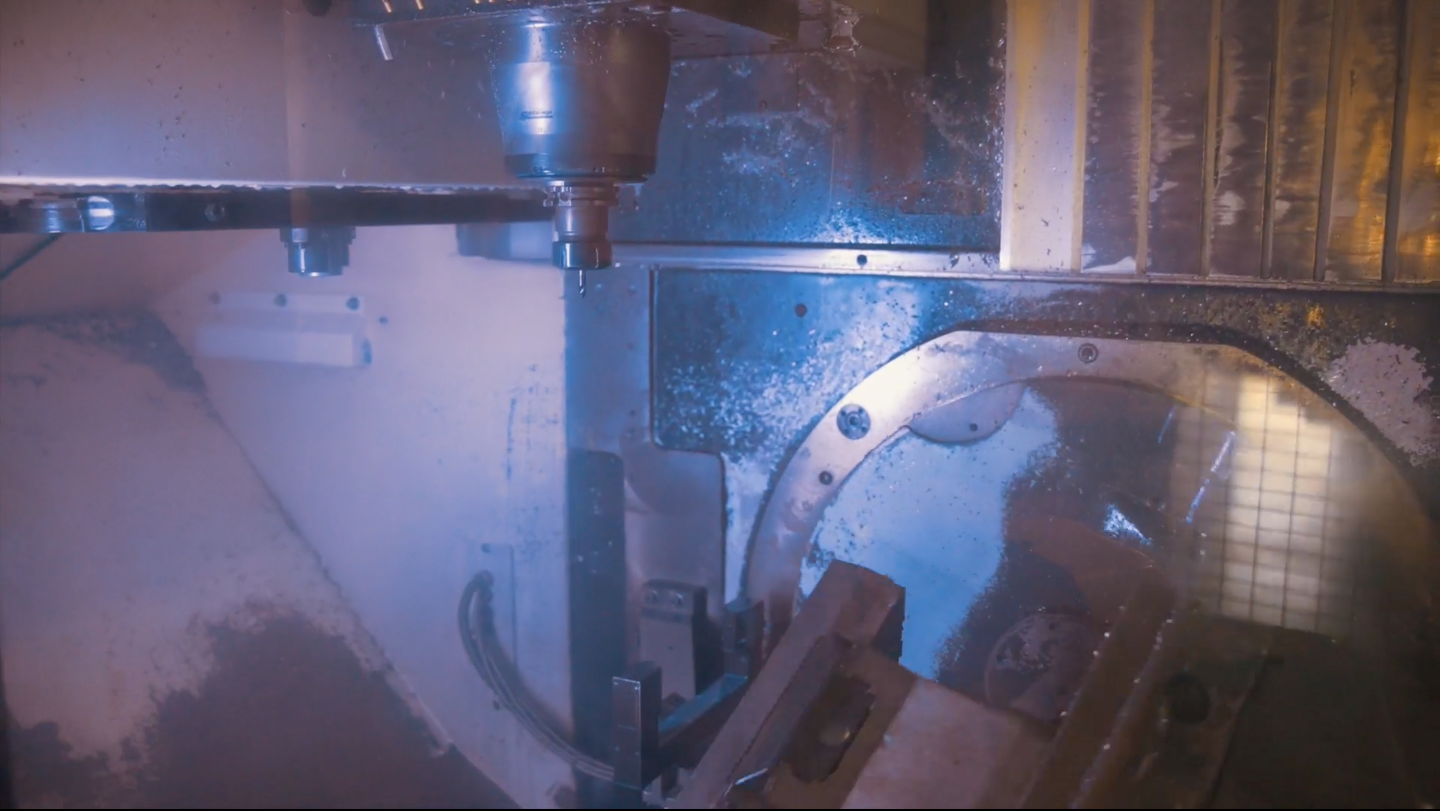
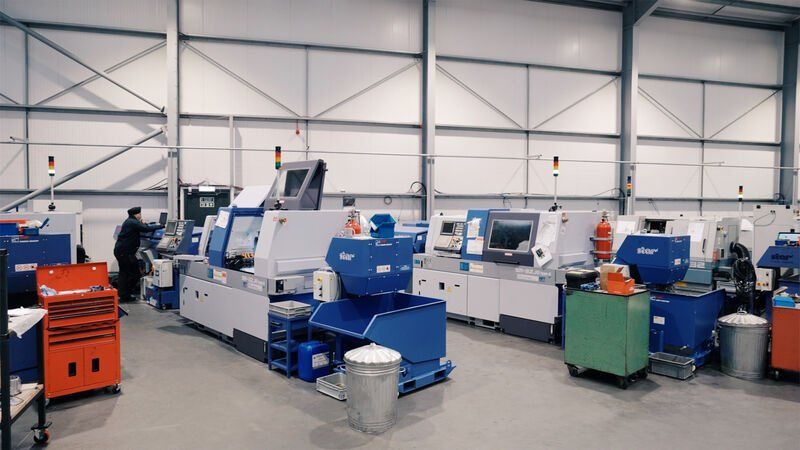
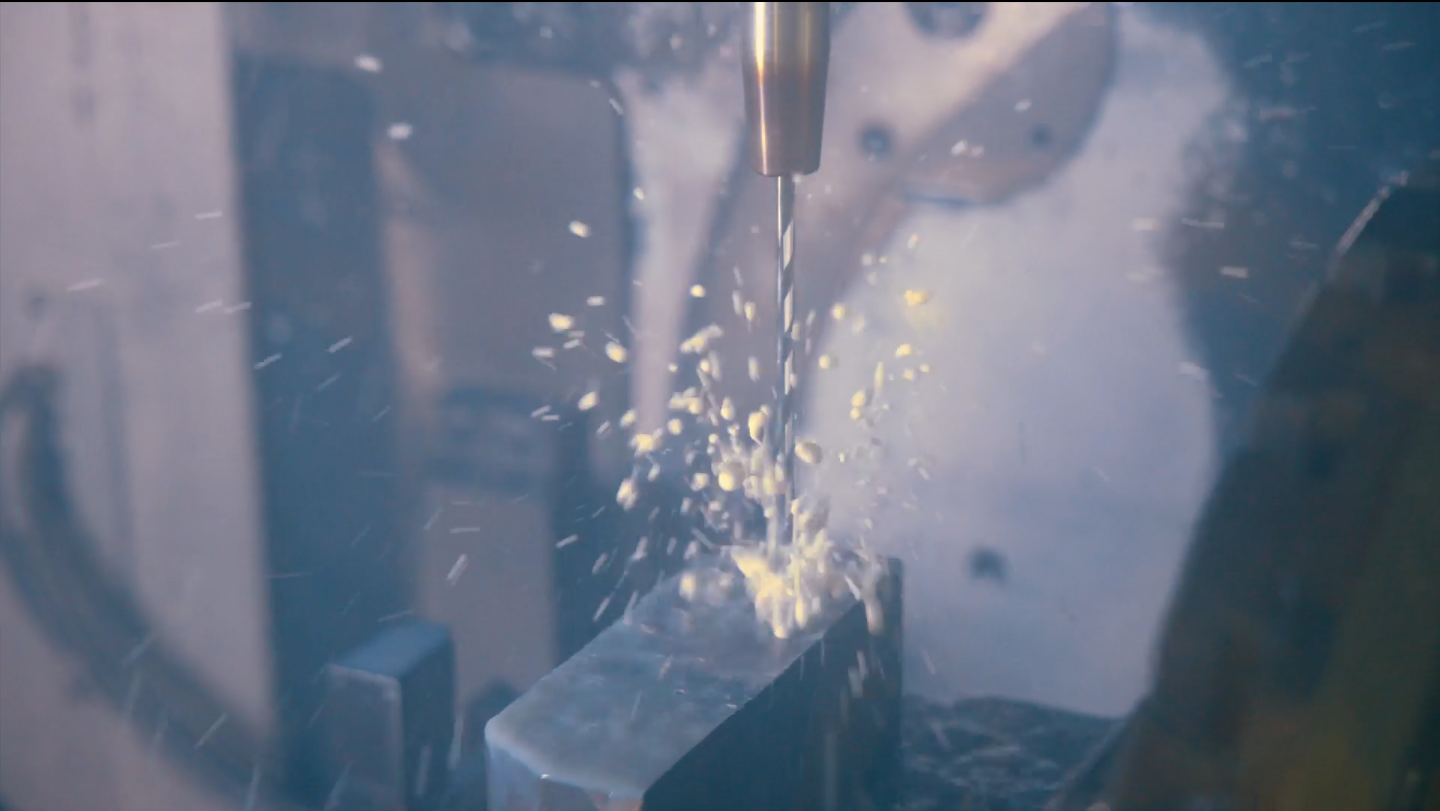
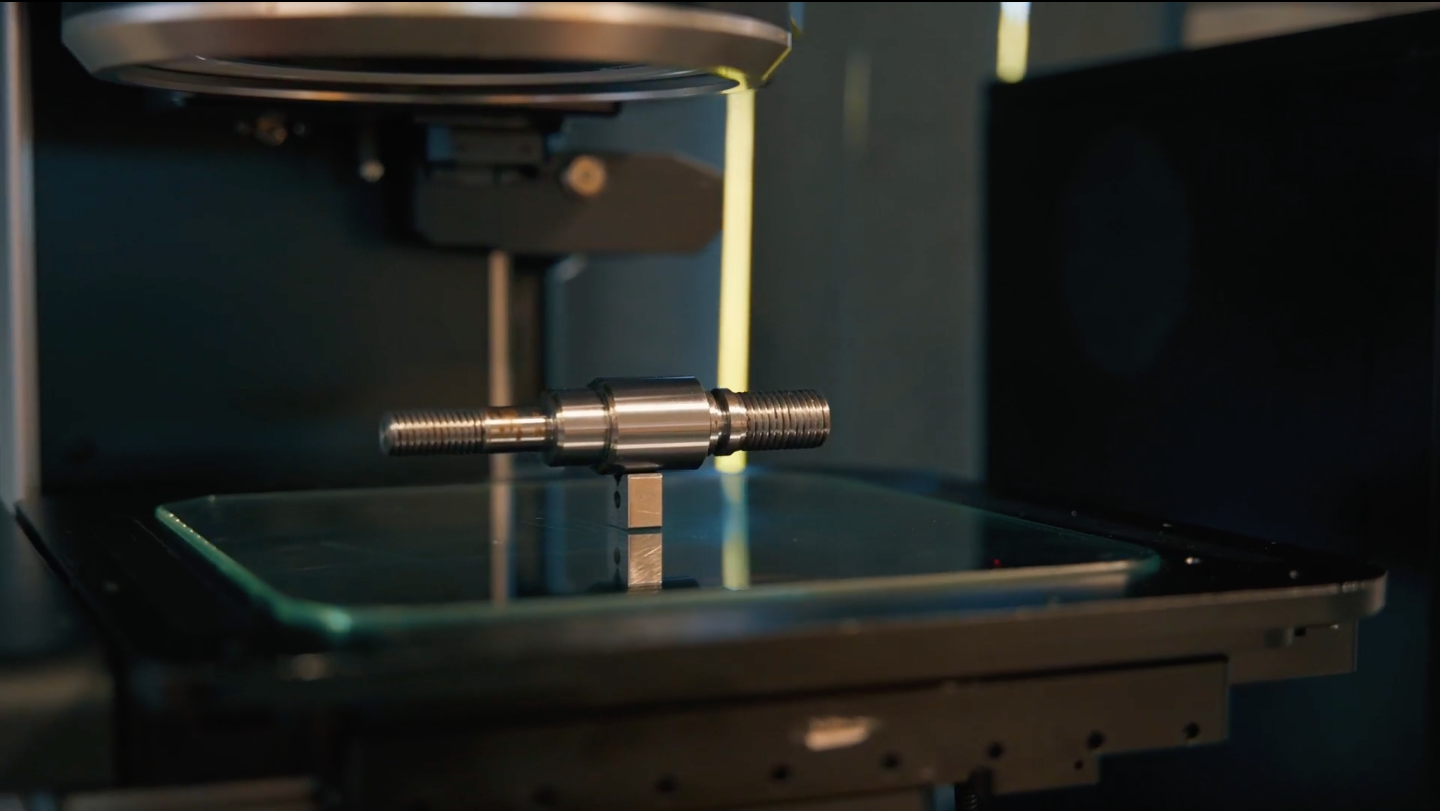